Budowa maszyn pneumatycznych opiera się na kilku kluczowych elementach, które współdziałają ze sobą, aby zapewnić efektywne działanie systemu. Na początku warto zwrócić uwagę na kompresor, który jest sercem całego układu. Jego zadaniem jest sprężanie powietrza, co pozwala na uzyskanie odpowiedniego ciśnienia niezbędnego do pracy innych komponentów. Kolejnym istotnym elementem są zbiorniki powietrza, które gromadzą sprężone powietrze i zapewniają jego stabilny dopływ do urządzeń roboczych. Rury i węże pneumatyczne stanowią połączenie między różnymi częściami systemu, umożliwiając transport sprężonego powietrza do siłowników i innych urządzeń. Siłowniki pneumatyczne to kluczowe elementy wykonawcze, które przekształcają energię sprężonego powietrza na ruch mechaniczny. Warto również wspomnieć o zaworach, które kontrolują przepływ powietrza w systemie, a także o filtrach, które oczyszczają powietrze z zanieczyszczeń.
Jakie są zalety i wady maszyn pneumatycznych
Maszyny pneumatyczne mają wiele zalet, które sprawiają, że są popularnym wyborem w różnych branżach przemysłowych. Jedną z głównych korzyści jest ich prostota konstrukcji oraz łatwość w obsłudze. Dzięki temu można je szybko wdrożyć do produkcji i zminimalizować czas przestoju. Dodatkowo maszyny te charakteryzują się dużą niezawodnością oraz niskimi kosztami eksploatacji. Sprężone powietrze jako medium robocze jest powszechnie dostępne i stosunkowo tanie, co czyni je ekonomicznym rozwiązaniem. Niemniej jednak istnieją również pewne wady związane z używaniem maszyn pneumatycznych. Przede wszystkim ich wydajność może być ograniczona przez straty ciśnienia w układzie oraz konieczność regularnej konserwacji komponentów, takich jak filtry czy zawory. Ponadto w przypadku awarii kompresora cały system może przestać działać, co prowadzi do przestojów w produkcji. Warto również zauważyć, że maszyny pneumatyczne mogą generować hałas podczas pracy, co może być problematyczne w niektórych środowiskach przemysłowych.
Jakie zastosowania mają maszyny pneumatyczne w przemyśle
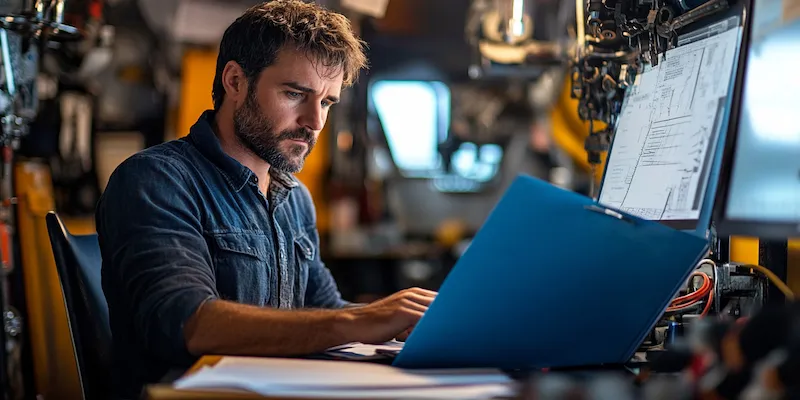
Maszyny pneumatyczne znajdują szerokie zastosowanie w różnych gałęziach przemysłu ze względu na swoją wszechstronność i efektywność. W branży produkcyjnej są wykorzystywane do automatyzacji procesów montażowych oraz pakowania produktów. Siłowniki pneumatyczne napędzają roboty przemysłowe, które wykonują precyzyjne operacje takie jak spawanie czy malowanie. W przemyśle spożywczym maszyny te służą do transportowania surowców oraz pakowania gotowych produktów, co przyspiesza procesy produkcyjne i zwiększa wydajność linii produkcyjnych. W sektorze motoryzacyjnym maszyny pneumatyczne są wykorzystywane do testowania komponentów oraz montażu pojazdów. W branży budowlanej natomiast znajdują zastosowanie w narzędziach takich jak młoty udarowe czy wiertarki pneumatyczne, które ułatwiają prace budowlane dzięki swojej mocy i wydajności. Dodatkowo maszyny pneumatyczne są również stosowane w medycynie do obsługi sprzętu diagnostycznego oraz terapeutycznego.
Jakie nowinki technologiczne dotyczą budowy maszyn pneumatycznych
W ostatnich latach obserwuje się dynamiczny rozwój technologii związanych z budową maszyn pneumatycznych, co wpływa na ich wydajność i funkcjonalność. Jednym z najważniejszych trendów jest automatyzacja procesów związanych z obsługą maszyn pneumatycznych. Dzięki zastosowaniu nowoczesnych systemów sterowania możliwe jest precyzyjne zarządzanie pracą siłowników oraz optymalizacja zużycia energii sprężonego powietrza. Kolejnym istotnym kierunkiem rozwoju jest miniaturyzacja komponentów pneumatycznych, co pozwala na tworzenie bardziej kompaktowych i lekkich rozwiązań dostosowanych do specyficznych potrzeb użytkowników. Innowacyjne materiały wykorzystywane do produkcji elementów maszyn zwiększają ich odporność na uszkodzenia oraz wydłużają żywotność urządzeń. Warto również zwrócić uwagę na rozwój technologii bezprzewodowej komunikacji między poszczególnymi elementami systemu, co umożliwia łatwiejszą integrację maszyn pneumatycznych z innymi systemami automatyki przemysłowej.
Jakie są kluczowe różnice między maszynami pneumatycznymi a hydraulicznymi
Maszyny pneumatyczne i hydrauliczne to dwa różne systemy, które wykorzystują różne media do przenoszenia energii i wykonywania pracy mechanicznej. Główną różnicą między nimi jest medium robocze: maszyny pneumatyczne używają sprężonego powietrza, podczas gdy maszyny hydrauliczne opierają się na cieczy, najczęściej oleju. Ta podstawowa różnica wpływa na wiele aspektów ich działania. Maszyny pneumatyczne są zazwyczaj lżejsze i bardziej kompaktowe, co sprawia, że są łatwiejsze w instalacji i mobilizacji. Z drugiej strony, systemy hydrauliczne oferują większą moc i precyzję, co czyni je idealnymi do zadań wymagających dużych sił, takich jak podnoszenie ciężkich ładunków. W kontekście kosztów eksploatacji, sprężone powietrze jest często tańsze w pozyskaniu niż olej hydrauliczny, jednak systemy pneumatyczne mogą być mniej wydajne w dłuższej perspektywie czasowej z powodu strat ciśnienia. Warto również zauważyć, że maszyny pneumatyczne są bardziej podatne na zmiany temperatury i wilgotności, co może wpływać na ich wydajność.
Jakie są najczęstsze problemy związane z maszynami pneumatycznymi
Podczas eksploatacji maszyn pneumatycznych mogą występować różnorodne problemy, które mogą wpływać na ich wydajność oraz niezawodność. Jednym z najczęstszych problemów jest wyciek sprężonego powietrza, który może prowadzić do znacznych strat energii oraz obniżenia efektywności całego systemu. Wyciek może występować w miejscach połączeń rur, zaworów czy uszczelek, dlatego regularna konserwacja i kontrola stanu technicznego komponentów są kluczowe dla utrzymania sprawności układu. Innym istotnym problemem jest zanieczyszczenie sprężonego powietrza, które może prowadzić do uszkodzenia elementów roboczych oraz obniżenia jakości produkcji. Dlatego stosowanie filtrów oraz separatorów wody jest niezbędne dla zapewnienia czystości medium roboczego. Dodatkowo niewłaściwe ustawienie ciśnienia roboczego może prowadzić do nieprawidłowego działania siłowników oraz innych komponentów. Warto również zwrócić uwagę na hałas generowany przez maszyny pneumatyczne, który może być uciążliwy w środowisku pracy.
Jakie są przyszłościowe kierunki rozwoju technologii pneumatycznych
Przyszłość technologii pneumatycznych zapowiada się bardzo obiecująco dzięki ciągłemu postępowi w dziedzinie automatyki i inżynierii materiałowej. Jednym z kluczowych kierunków rozwoju jest integracja maszyn pneumatycznych z systemami IoT (Internet of Things), co umożliwi zdalne monitorowanie i zarządzanie procesami produkcyjnymi. Dzięki zastosowaniu czujników i inteligentnych algorytmów możliwe będzie optymalizowanie zużycia energii oraz przewidywanie awarii jeszcze przed ich wystąpieniem. Kolejnym ważnym trendem jest rozwój materiałów kompozytowych oraz nanotechnologii, które mogą przyczynić się do zwiększenia wydajności i trwałości komponentów pneumatycznych. Innowacyjne rozwiązania w zakresie automatyzacji pozwolą na jeszcze szybsze i bardziej precyzyjne operacje, co zwiększy konkurencyjność przedsiębiorstw korzystających z technologii pneumatycznych. Ponadto rosnące zainteresowanie zrównoważonym rozwojem skłania producentów do poszukiwania ekologicznych rozwiązań w zakresie sprężania powietrza oraz minimalizacji odpadów produkcyjnych.
Jakie są kluczowe aspekty bezpieczeństwa w użytkowaniu maszyn pneumatycznych
Bezpieczeństwo użytkowania maszyn pneumatycznych jest niezwykle istotnym zagadnieniem, które powinno być priorytetem dla każdego przedsiębiorstwa korzystającego z tego typu technologii. Kluczowym aspektem jest odpowiednie szkolenie pracowników obsługujących maszyny pneumatyczne, które powinno obejmować zarówno teoretyczne zagadnienia dotyczące budowy i działania urządzeń, jak i praktyczne umiejętności związane z ich obsługą. Ważne jest również przestrzeganie zasad BHP oraz stosowanie odpowiednich środków ochrony osobistej, takich jak rękawice czy okulary ochronne, aby minimalizować ryzyko urazów podczas pracy z maszynami. Regularne przeglądy techniczne oraz konserwacja urządzeń są niezbędne dla zapewnienia ich sprawności oraz bezpieczeństwa użytkowania. Należy także zwrócić uwagę na właściwe oznakowanie stref niebezpiecznych oraz stosowanie zabezpieczeń mechanicznych, takich jak osłony czy blokady, które chronią pracowników przed przypadkowymi urazami. Warto również wdrożyć procedury awaryjne na wypadek wystąpienia nieprzewidzianych sytuacji związanych z działaniem maszyn pneumatycznych.
Jakie są koszty związane z budową maszyn pneumatycznych
Koszty związane z budową maszyn pneumatycznych mogą się znacznie różnić w zależności od wielu czynników, takich jak rodzaj zastosowanych komponentów, skomplikowanie konstrukcji czy specyfika aplikacji przemysłowej. Na początku warto uwzględnić koszty zakupu podstawowych elementów systemu, takich jak kompresory, zbiorniki powietrza, siłowniki czy zawory. Ceny tych komponentów mogą się różnić w zależności od producenta oraz jakości wykonania. Kolejnym istotnym aspektem są koszty instalacji oraz uruchomienia systemu pneumatycznego, które mogą obejmować prace montażowe oraz dostosowanie infrastruktury zakładu do wymogów nowej technologii. Nie można zapominać o kosztach eksploatacyjnych związanych z utrzymaniem systemu w dobrym stanie technicznym; regularna konserwacja oraz wymiana zużytych części to dodatkowe wydatki, które należy uwzględnić w budżecie firmy.
Jakie są przykłady zastosowań maszyn pneumatycznych w codziennym życiu
Maszyny pneumatyczne znajdują zastosowanie nie tylko w przemyśle, ale również w wielu aspektach codziennego życia. Przykładem mogą być narzędzia pneumatyczne używane przez rzemieślników i majsterkowiczów do wykonywania różnych prac budowlanych czy remontowych. Młoty udarowe czy pistolety do malowania to tylko niektóre z narzędzi wykorzystujących sprężone powietrze do ułatwienia pracy użytkowników. W branży motoryzacyjnej maszyny pneumatyczne są wykorzystywane do obsługi warsztatowej; podnośniki pneumatyczne umożliwiają szybkie podnoszenie pojazdów podczas naprawy lub konserwacji. Również wiele urządzeń gospodarstwa domowego korzysta z technologii pneumatycznej; odkurzacze przemysłowe często wykorzystują sprężone powietrze do efektywnego zbierania kurzu i brudu. W medycynie maszyny te znajdują zastosowanie w sprzęcie diagnostycznym oraz terapeutycznym; przykładem mogą być urządzenia do nebulizacji leków czy aparatura do analizy medycznej.